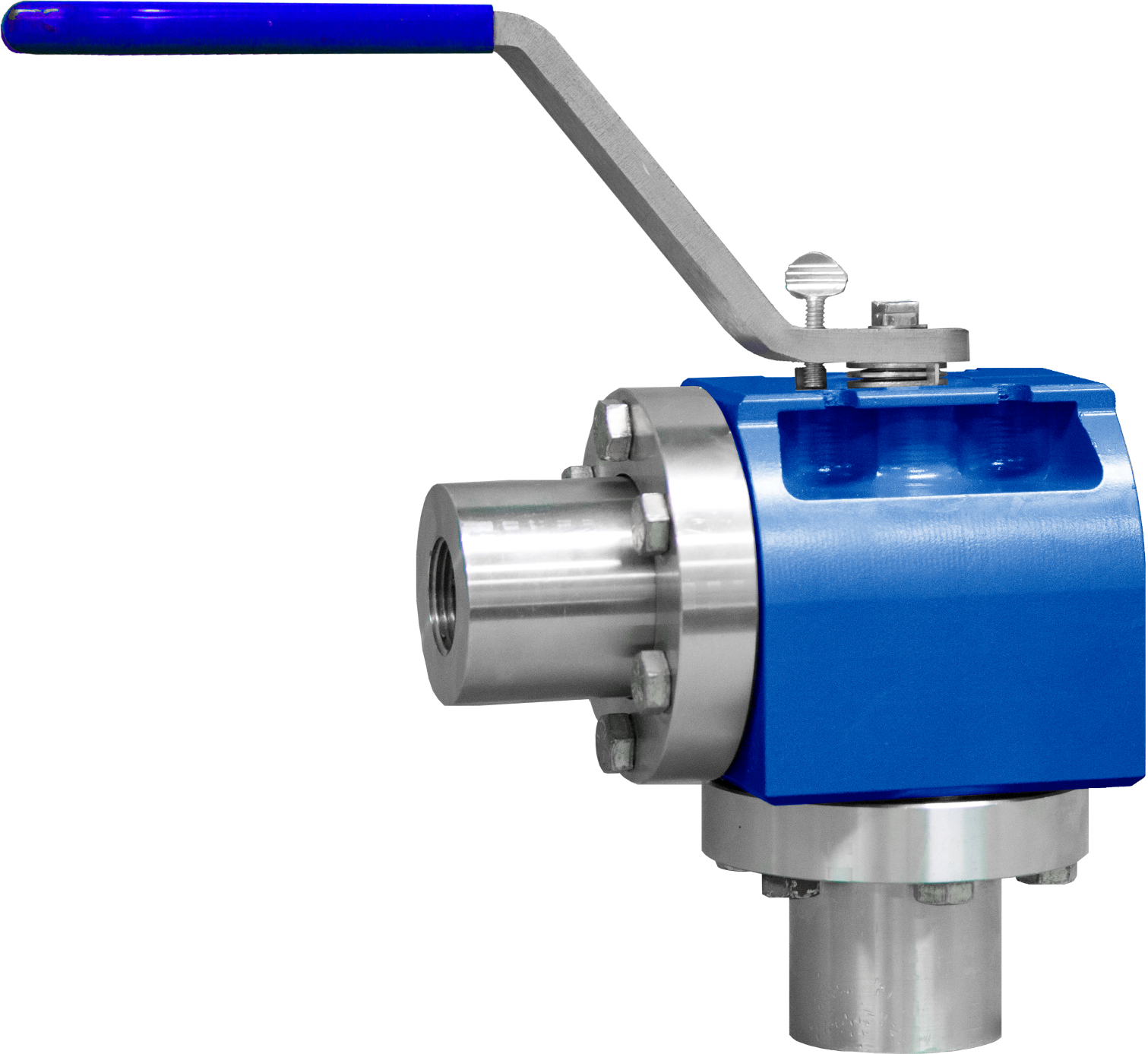
The Twin Disc Valve was initially designed to manage injection fluids in Enhanced Oil Recovery (EOR) projects, as well as to control the production of crude oil and natural gas wells. It can also be used in other applications such as gas lift, gas-assisted plunger lift, and corrosive slurry, essentially any situation that requires the management of high-pressure fluids. As flow or pressure is regulated, wear is inevitable in any throttling valve. This typically occurs on the surface and around the controlling orifice, especially in globe, gate, butterfly, ball, and plug valves. However, in the Twin Disc, the control surfaces and seal surfaces are distinct. The controlling orifice exposes the smallest amount of control surface compared to other valve types. There are no obstructive shapes in the flow path, which are common in globe style and “needle and seat” valves. As a result, the Twin Disc experiences minimal wear on the throttling and shut-off area. The differential pressure across the discs secures them together, providing a stable control mechanism. There are no loose or unsupported parts that could lead to vibration, noise, or fatigue failures. Each time the valve is rotated, the exposed part of the disc’s surface is cleaned of foreign deposits.
Download PDF Brochures:
Features
- Quarter-turn valves (90ᵒ full on/off)
- Actuated or Manual
- MOV Choke
- Hub design allows replacement of repair parts without breaking pipe or actuator connections
- Direct mount of actuator to valve body
- Standard ISO/DIN bolting pattern
- 5,000 MAWP
- 100% hydro-testing of all assemblies
- Low torque ratings
Applications
- Liquid & Gas Pressure or Flow Control
- Throttling Valve
- Gas Storage
- Gas Lift Surface Choke
- Pump Startup
- Heated Separators
- Separator Dump Valve
- Water & Gas Injection
- Disposal Wells
Additional Info
- Accessories: Stellite wear sleeve, Multistage pressure drop utilizing fixed orifice beans.
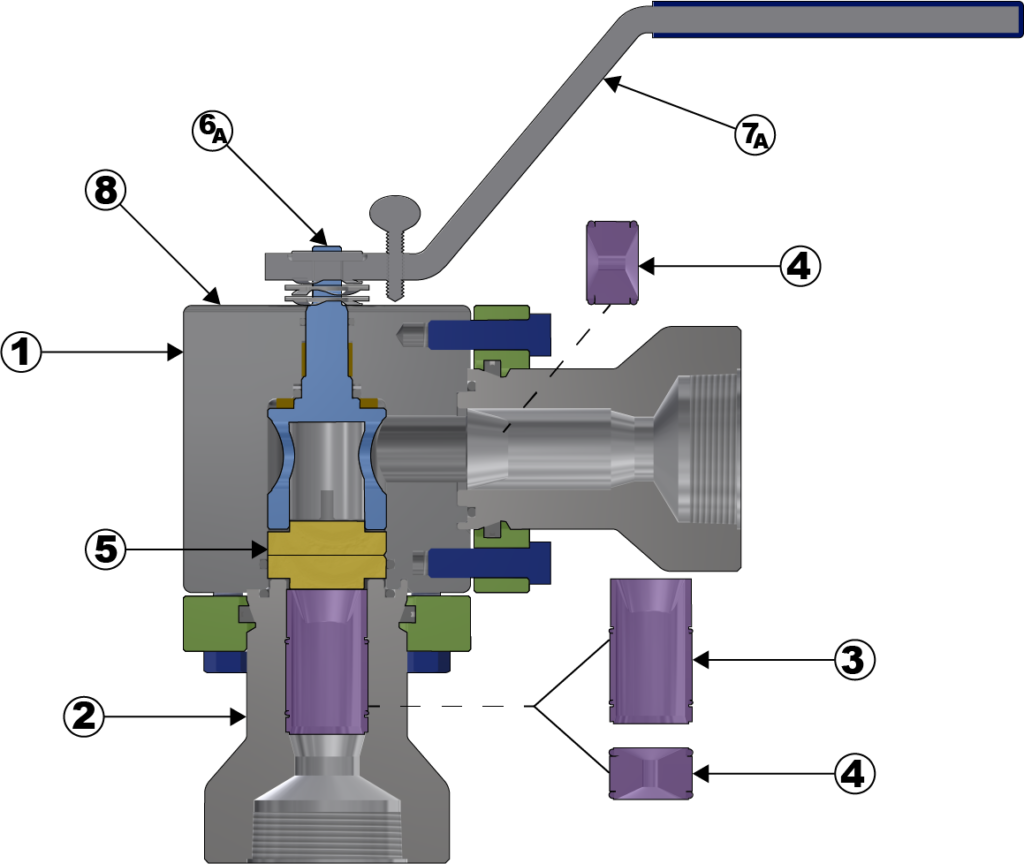
HCA Advanced Features
- Valve Body: Durable and corrosion-resistant 316 stainless material.
- Hub Assembly: Allows easy access to internals without breaking pipe connections, disconnecting or recalibrating the actuator. The design allows for less expensive replacement of the downstream hub in lieu of replacing the whole valve body.
- Wear Sleeve (Optional): All valve hubs allow for wear sleeves. The wear sleeve is made from a durable Stellite material for abrasive or turbulent environments extending valve life.
- Fixed Orifice Bean (Optional): The Hydra design allows for placement of a Fixed Orifice Bean to achieve up to a 2 stage (HCI) or 3 stage (HCA/HCY/CSX) pressure drop within the valve. The fixed orifice bean also extends the life of the valve.
- MOV Trim: All valves come standard with Tungsten Carbide Trim available in sizes up to 3/4”.
- Rotator: The smaller rotator outside diameter reduces operating torque, requiring smaller and less expensive actuators.
6A.* Stem Assembly: The smaller shaft diameter reduces operating torque, requiring smaller and less expensive actuators. - Manual Handle: The handle and rotator are specially designed to resist thread pull out.
7A.* Manual Handle (Optional): The thumb screw on the handle will resist movement of the stem until released. - Calibration Plate: Handle equipped with indicator pointing to a Calibration Plate showing percentage and # of 64ths open.
- Actuator Mounting (Optional – Not Shown): Design allows for mounting of common valve actuators with a simplified system to reduce hysteresis.