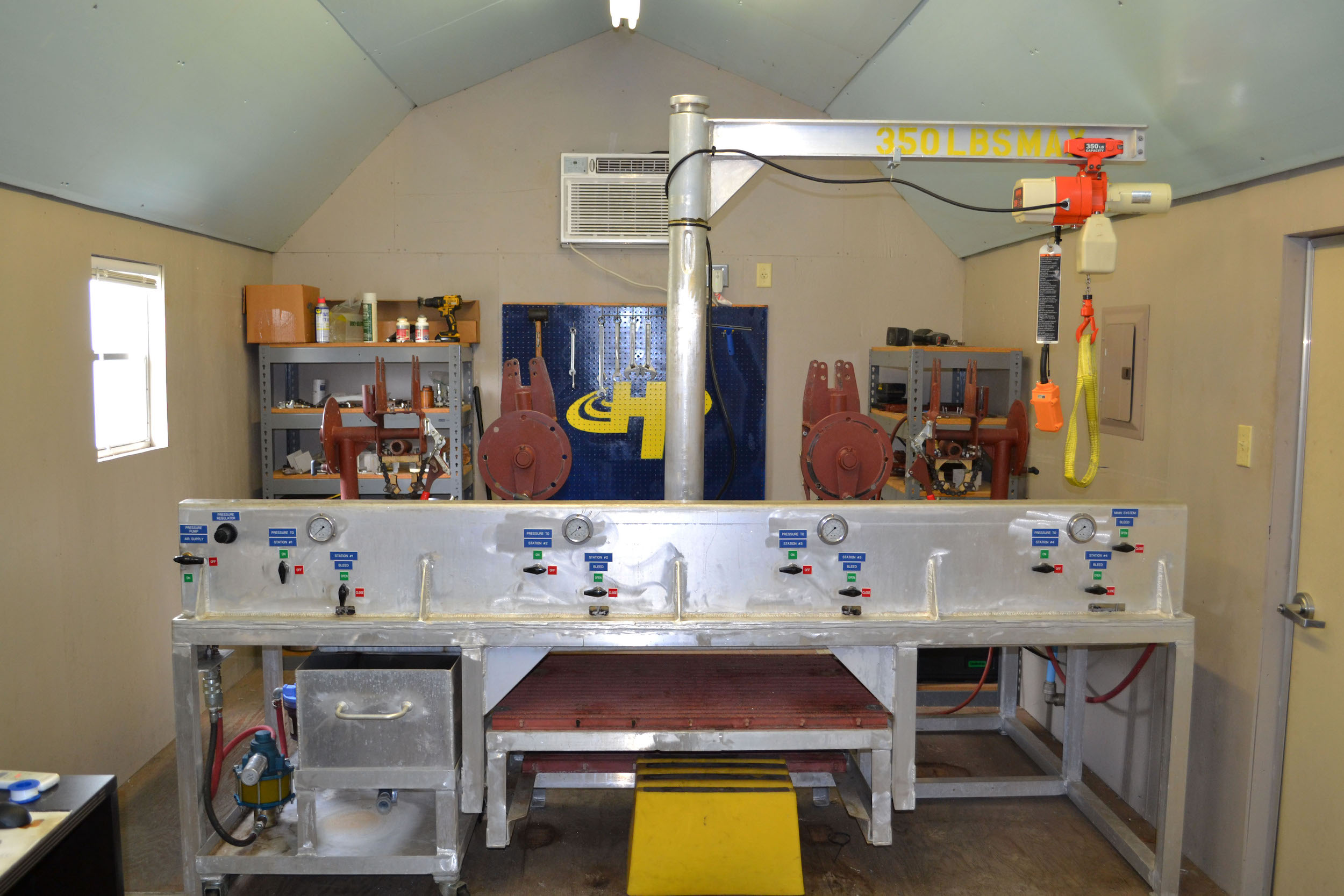
Valve Testing Facility
Quality control is the cornerstone of our valve manufacturing process; quality is crucial to the success of our products. Our clients depend on the performance of our valves for their operations to run safely and efficiently. We conduct rigorous testing on every Hydroplex valve to ensure adherence to our manufacturing standards and design specifications before it leaves our facility.
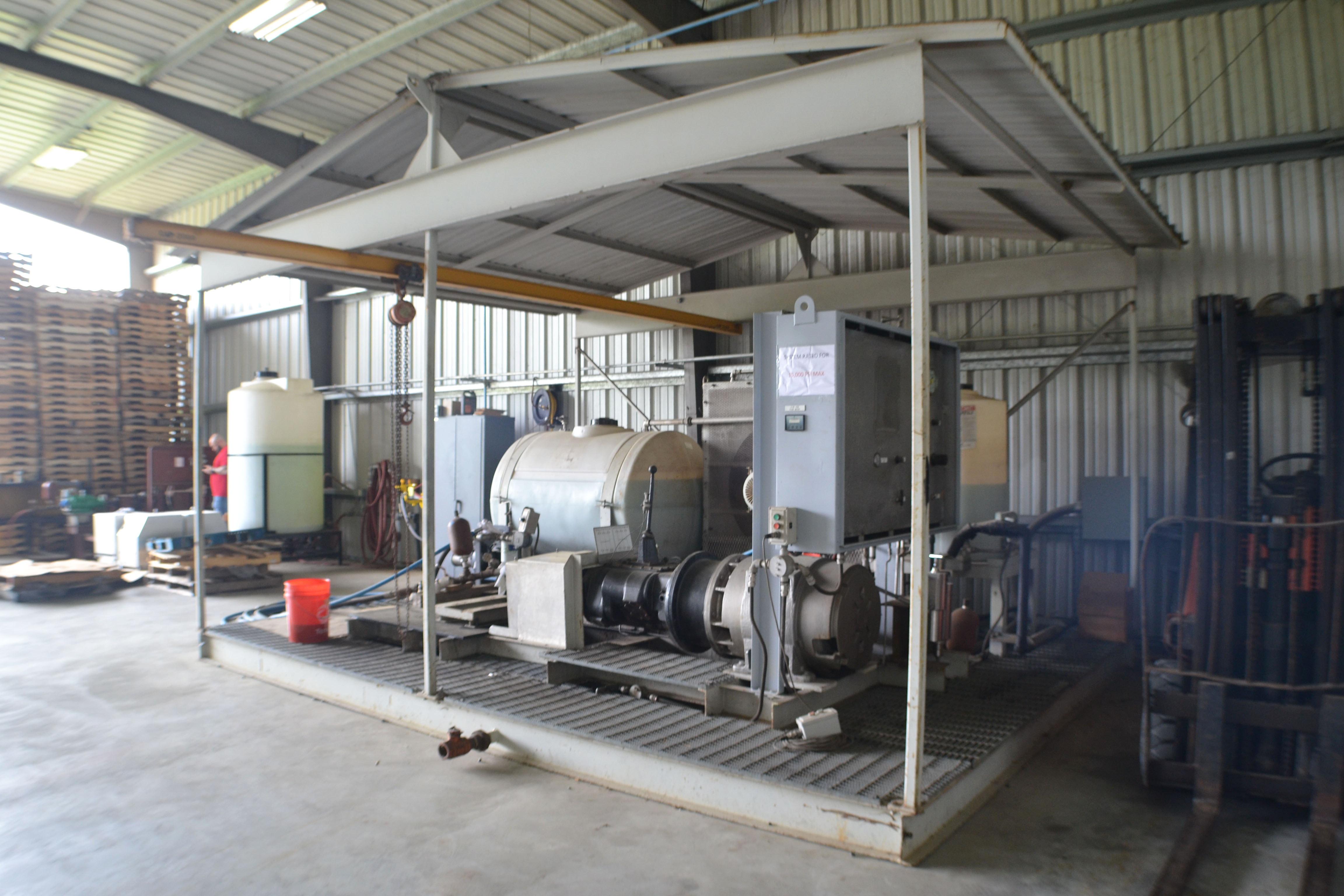
Our state-of-the-art Hydroplex testing facility, as shown in the photographs, is comprised of a custom four-place valve test bench, proprietary test software, a data acquisition station, and a laser label printer. The system is equipped to perform an API 6A PSL1 hydrostatic shell test on our throttling valves and a seat leakage test to confirm the product complies with ANSI/FCI 70-2 Class IV leakage requirements for Control Valves. The high pressure test is performed at 1.5 times maximum allowable pressure.
Integrated Testing System
Our testing process, documentation, and labeling are all part of the digitally controlled, integrated system. Upon completion of a test, the results are stored electronically in the data acquisition system as a permanent record. Hydroplex also emails copies of the actual test results to the client in a document packet. These records detail who built and tested the valve, its serial number, and a step-by-step digital graph of the test results for each valve.
Guided by our ISO 9001-2015 certified quality management system, we ensure our products meet the high-quality standards developed by Hydroplex prior to being shipped to our clients.
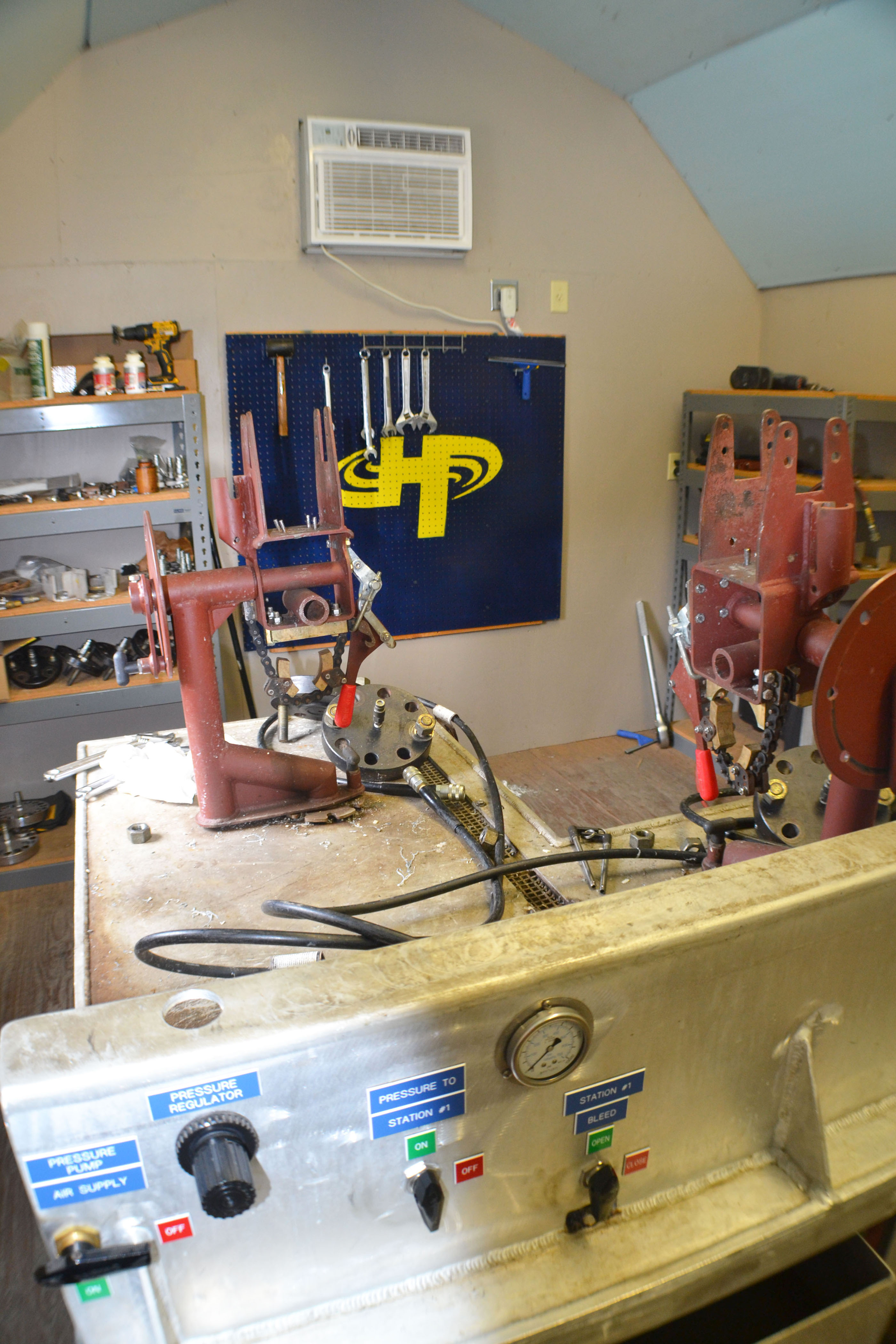