What is a Class II Injection Well and what is the intended purpose?
Class II injection wells are an underground injection control (UIC) well regulated by the U.S. Environmental Protection Agency (EPA). These wells are used to inject fluids associated with oil and gas production into underground formations that contain oil or natural gas, or that are suitable for fluid disposal or storage. The main purposes of Class II injection wells are to enhance the recovery of oil and natural gas, or to dispose of the saltwater (brine) and other fluids that are produced along with the hydrocarbons. Class II injection wells can also be used to store hydrocarbons that have been extracted from other sources, such as natural gas liquids or liquefied petroleum gas (LPG).
Types of Class II Injection Wells
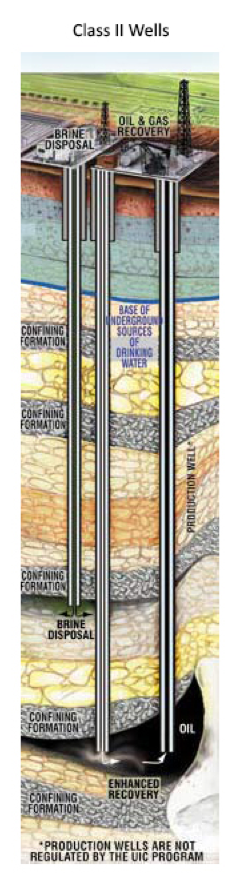
There are three types of Class II injection wells, depending on the type of fluid injected and the purpose of the injection. These are:
Enhanced recovery wells: These wells inject fluids, such as water, steam, carbon dioxide, or nitrogen, into oil or natural gas reservoirs to increase the pressure and improve the flow of the hydrocarbons to the surface. Enhanced recovery wells can also be used to recover residual oil or natural gas that remains in the formation after primary or secondary recovery methods have been exhausted. Enhanced recovery wells are the most common type of Class II injection wells, accounting for about 80% of all Class II wells.
Saltwater disposal wells: These wells inject saltwater (brine) and other byproducts resulting from oil and natural gas production into underground formations, accounting for about 20% of all Class II wells.
Hydrocarbon storage wells: These wells inject hydrocarbons that have been extracted from other sources, such as natural gas liquids or liquefied petroleum gas, into underground formations that are suitable for storage. Hydrocarbon storage wells are used to store these fluids until they are needed for transportation, distribution, or consumption. Hydrocarbon storage wells are the least common type of Class II injection wells, accounting for less than 1% of all Class II wells.
Saltwater Disposal (SWD)
These wells inject saltwater (brine) and other fluid byproducts resulting from Oil and Natural Gas production, into underground formations that are not used for sources of drinking water or hydrocarbon production. Saltwater disposal wells are the second most common type of Class II injection wells, accounting for about 20% of all Class II wells.
Saltwater disposal (SWD) wells are predominantly located in states with substantial oil and gas production. The primary locations with a high concentration of these wells in the United States include:
Texas: The state has the highest number of SWD wells in the country, with over 54,000. These wells are used to dispose of the large volumes of produced water generated by the oil and gas industry in Texas, especially from the Permian Basin and Eagle Ford Shale regions.
Oklahoma: The state has over 10,000 SWD wells, which are mainly concentrated in the Anadarko Basin and the SCOOP/STACK plays. These wells inject the produced water from oil and gas activities into deep underground formations. The state has faced challenges with induced seismicity linked to these wells, prompting regulatory actions to monitor and control the injection volumes and locations.
Kansas: The state has more than 8,000 SWD wells, which are mostly located in the western and central parts of the state. These wells receive the produced water from the oil and gas fields in Kansas, as well as from neighboring states like Colorado and Nebraska. Kansas, like Oklahoma, has experienced induced seismicity associated with these disposal wells.
California: With its large oil fields, California utilizes SWD wells to manage the produced water from oil extraction. These wells are regulated to ensure they do not impact drinking water sources.
North Dakota: The state has numerous SWD wells, particularly in areas like the Bakken Shale, which is a significant oil-producing region.
Ohio: The state has over 200 SWD wells, which are primarily used to dispose of the produced water from the Utica Shale and Marcellus Shale operations in Ohio and Pennsylvania.
Other states with notable numbers of SWD wells include Colorado, New Mexico, Wyoming, and Louisiana.
Why a Hydroplex valve?
In high-pressure liquid applications within the oil and gas sector, such as brine water injection, it is imperative to choose the appropriate control valve for maintaining safety, reliability, and operational efficiency. Hydroplex throttling valves are engineered to control flow or pressure in these demanding environments. Their ability to precisely throttle makes them ideal for circumstances where frequent flow adjustments or consistent flow rates are required. This functionality is crucial in Saltwater Disposal (SWD) wells, where managing injection rate and pressure is essential for optimizing disposal activities, ensuring pump performance, and maintaining well integrity.
Hydroplex valves are designed to function in the high differential pressure conditions frequently found in SWD operations. They operate at differential pressures ranging from a few PSI to several thousand PSI, making them suitable for the intense conditions of SWD wells. Additionally, Hydroplex valves can be configured internally with multistage pressure drops to reduce noise and/or cavitation experienced in the control process.
Constructed from robust materials like stainless steel or alloy steel, Hydroplex valves are built to withstand the erosive or corrosive conditions encountered in SWD both from external exposure and internal process environments.
The Hydroplex Twin Disc valves are known for their quick shut-off capability while providing a tight ANSI Class IV seal with a simple quarter-turn motion. The Hydroplex products are suitable for both on/off and throttling services making them a good choice for shutoff, dumping, and control applications in high-pressure systems.
It’s important to consider the specific requirements of your application, including the pressure, flow rate, temperature, and chemical composition of the brine water, when selecting a throttling valve. Consulting with Hydroplex specialists is recommended to ensure the selected valve meets all operational needs. Complete the Hydroplex Valve Quote Request form for your application and a Hydroplex technical representative will contact you. Remember, the right valve not only improves the performance but also extends service life and optimizes production capabilities of the system. In summary, Hydroplex throttling valves offer precise control, durability, and reliability for SWD applications.